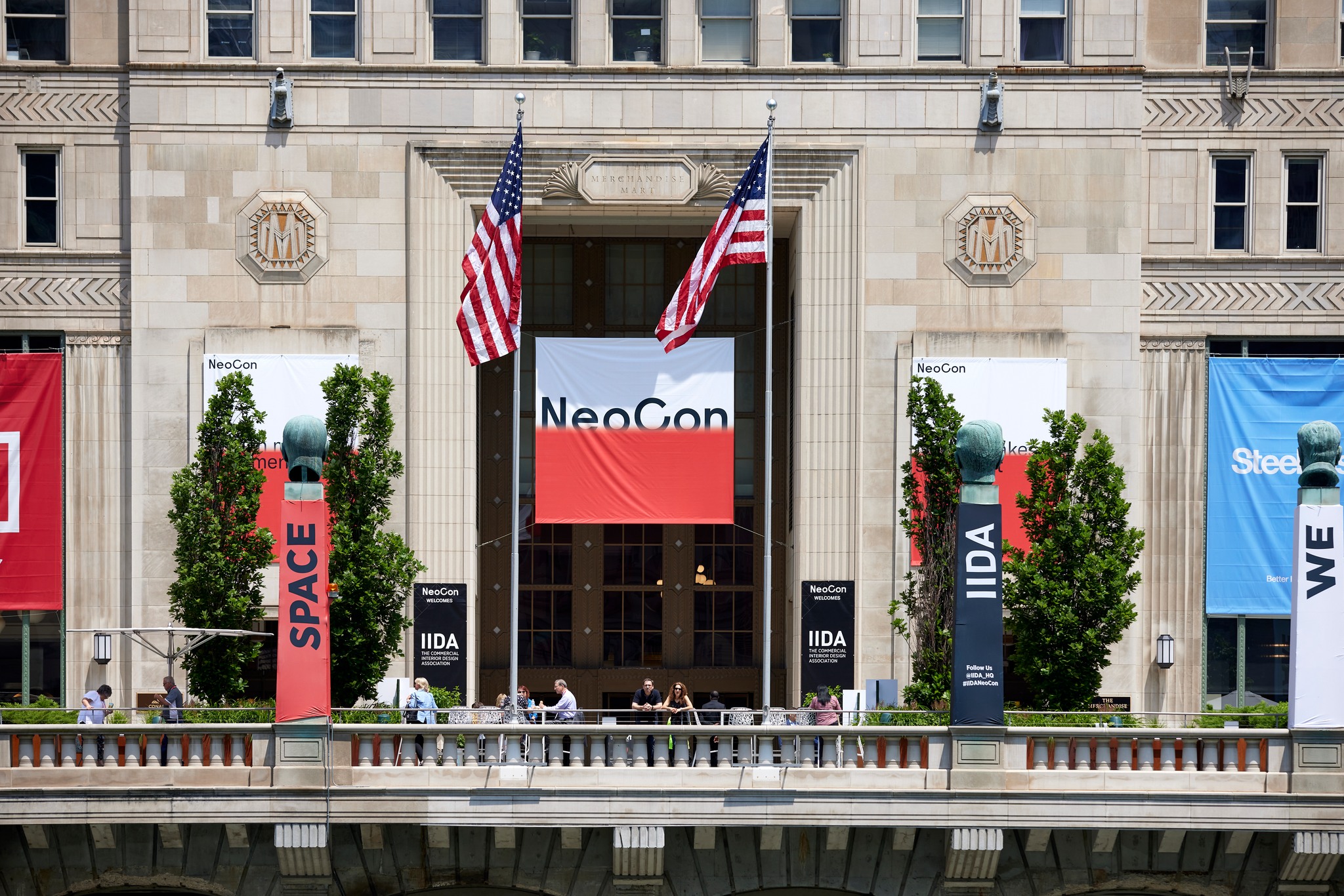
In arista we have different allies that provide us with solutions to create extraordinary spaces prepared for the future. For this, each one is focused on producing products of the highest quality, ensuring their proper functioning with the use and over the passage of time. Haworth is no exception. Their products are subjected to a series of extreme tests, including high temperatures, simulators and more. Join us in this article and let's dive into the Haworth Test Lab.
"If they can handle this, there won't be any problems," says Dezi Noteboom, a test lab supervisor who has worked at the lab for more than 35 years. Their job is to push products to the limit, to make sure they work to our high standards. The goal is to predict faults and correct them before they reach the customer." -Haworth
Haworth's test lab conducts over 1800 tests each year; and each of these includes up to 15 exams of 1 week duration. It has special facilities for electrical tests, recognized by Intertek, which endorses its procedures and ensures that the results will reach the highest standards in the market. The rest of its laboratories are A2LA accredited.
Extreme temperature testing
One of the factors that weakens the products the most is temperature. Therefore, the brand has cameras that simulate extreme dry heat, high humidity and glacial cold. The chambers can heat up to 120°F. and can change to 90% humidity.
Inside these chambers, furniture spends days or even a week, checking the material, fabric and adhesives and how they withstand these conditions. The cameras are also used to test for aging fabrics, sunscreens and tiles by creating the damaging effects of sunlight and rain over time. "We want to make sure that we won't have a problem with our products breaking down once they go out into the field, whether it's from UV rays coming in through windows or sitting directly in sunlight," Noteboom said.
Tests to measure durability
Much of Haworth's lab is dedicated to durability testing: in which the products, whether chairs, cabinets or adjustable tables, are placed in machines that move, push and rotate them. Also, a weight of 125 pounds is dropped on the edge of the chair approximately 100,000 times. In BIFMA testing, weight is dropped in the center of the seat, but Haworth seeks to better represent the actual use of the chair by dropping the weight on the edges of the product.
Products are tested at different stages of the development process and again before they are ready to be launched on the market.
Final tests
The products also undergo a series of tests with liquids or materials that stain, from markers, to mustard. This serves Haworth for instructions in user and maintenance guide manuals. To make more realistic tests, the stains are left for up to an hour before being cleaned.
"We've built a reputation for going above and beyond. The testing lab is an essential part of our commitment to making sure our products meet and exceed those high standards for our customers. " -Haworth
This is a sample of the rigorous manufacturing and quality assurance processes that our allies have, we are sure that their products will elevate the aesthetics and functionality of their facilities for a long time. If you want to know more about our wide range of products available for import, contact us.